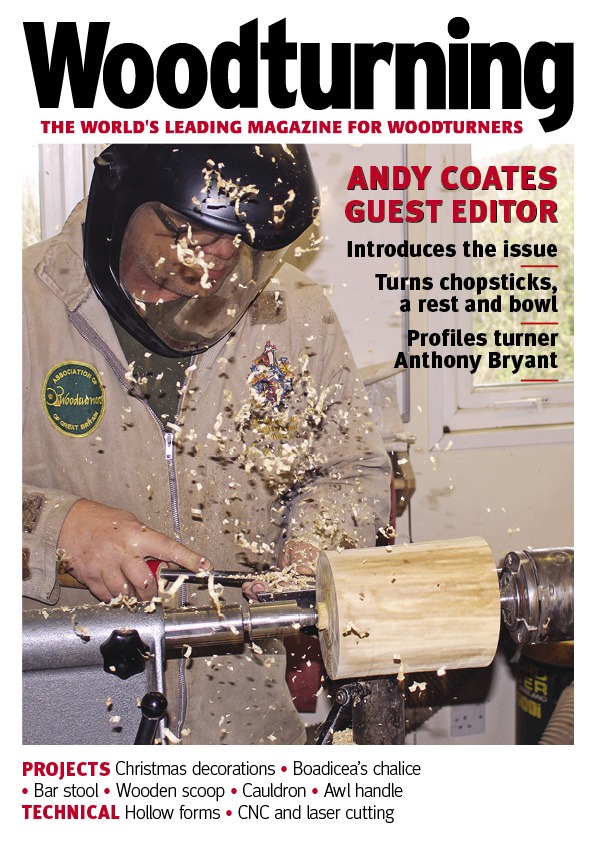
A lathe may not have a tool rest. You will need to adjust its angle to compensate for your hands' awkward position. Flat spots on many tool rests allow your fingers to slide back and forth. Some are adjustable and fit most lathes, while others have multiple height settings. These are the important things to look at when purchasing a tool rest for your Lathe.
Light source
You're not the only one who isn't familiar with the idea of a light source to power a tool rest on a lathe. Many lathes are equipped with overhead room lighting, as well as fixtures that are attached to the ceiling or headstock. These lights add additional lighting but can block access for operators. A tool rest that features an integrated light source is the best choice for a larger lathe.
A lathe tool rest includes a vertical and horizontal post. The tool arm has a light source on its front, which is usually an LED illumination strip. The wire 20 attaches the strip to an electricity source. Alternatively, a tool rest without a light source is provided. This invention will make it possible to design a tool rest for a lathe which includes a lighting source.
Support element
Support element to tool rest for lathe solves many problems related unexpected movement of toolrest. In the prior art, the support element for the toolrest is a point-to–point abutting arrangement. Because the toolrest must bear torque and axial force during tooling, the friction force generated is not adequate to support the toolrest. This design poses safety issues. The Support element for tool rest for the lathe protects the toolrest from torque and axial force generated during tooling.
A toolrest is a piece of metal that stands on its own. The bar is used to provide restraint. It may also have grooves for positioning the tool. Some models come with a handle for guiding the tool as it turns. These toolrests are made of either metal or wooden. Smoothen any wooden toolrests. A support element for a tool rest for lathe can be purchased separately.
Adaptive device
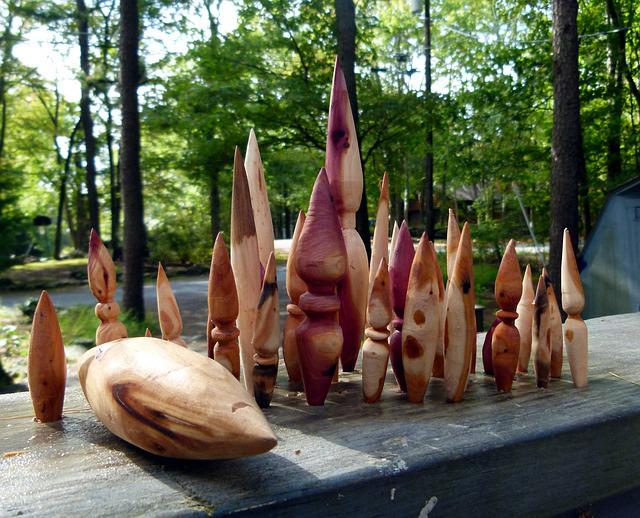
The adaptive device 100 is an outer cylindrical sleeve with an attached threaded segment and a header. It also has a threaded head. The shoulder 140 is milled to form a flat surface 160 that can hold set screws 370 in lathe holder 311. The set screw 370 is pressed against the flat side 160 to secure the adaptive device within the lathe.
The Mortimer pinrest claims it has a gated function. However, the support bar rides parallel to the tool shaft. This should allow for sufficient levering ability. This device has a very large gate, which almost certainly suffers cam locking. This is a significant improvement on a standard tool rest but it does not offer much in the way of motion restriction or fine tool control. It is not a good choice for those who need complete tool control without sacrificing precision.
Use a cutting tool
If you are new to lathe work, the first thing you'll want to consider is purchasing a cutting tool rest for your lathe. This accessory allows you to hold your tool as close to wood as possible during its rotation. A toolrest's body is sloped from the forward edge to allow you to position your tool at the best angle for cutting. You can smoothen the surface of your cutting tool rest by using a file.
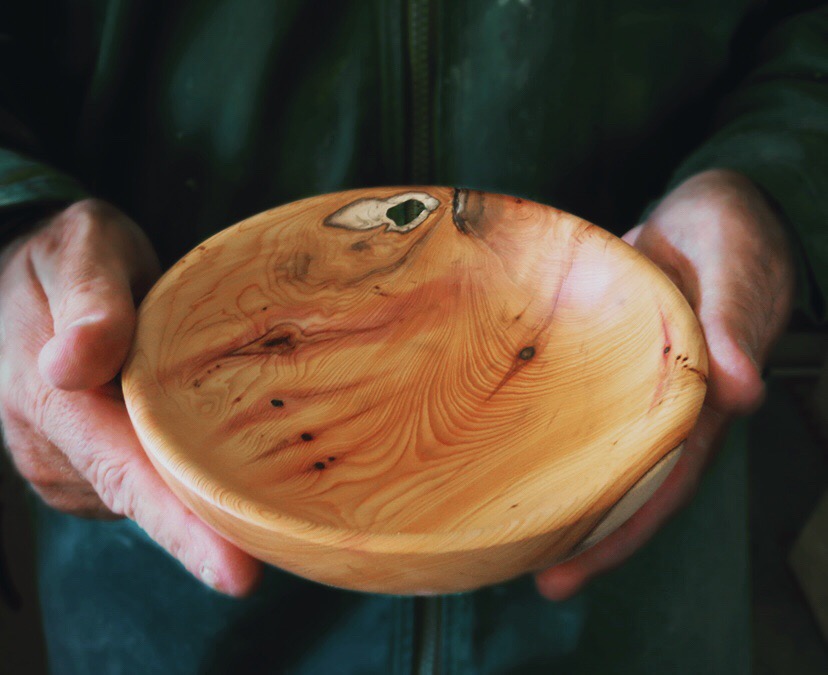
If you are looking for a cutting-tool rest for your lathe make sure it has flat spots. This will prevent your fingers from rubbing against the surface. This type of tool rest is ideal for handwork as it prevents your hands slipping off the cutting tools. It is also useful for keeping the workpiece stable during high-speed turning. There are various sizes to suit your lathe. You can ask a professional to assist you in making a choice.
FAQ
Can I make my living doing this job?
Yes! Many woodworkers are already doing so. According to the U.S. Bureau of Labor Statistics in May 2012, the median annual income for woodworkers was $34,000 This is more than the national average of 31,000 per annum.
How can a beginner woodworker make money?
Many people want to open an online furniture business and are learning how to build it. If you are just starting to build furniture, there are many other ways to make money than selling on Etsy. Sell at craft fairs or other local events. You could also offer workshops to help others learn how to make their own furniture. You might be able to offer services like remodeling homes or making custom pieces for clients if you are a skilled carpenter.
What is the average time it takes to finish furniture?
It depends on what size piece of furniture you have. Smaller projects like boxes and picture frames can be finished within one day. Larger projects, like desks or dining tables require several days. It takes time to properly stain and seal wood.
Statistics
- Most woodworkers agree that lumber moisture needs to be under 10% for building furniture. (woodandshop.com)
- Woodworkers on the lower end of that spectrum, the bottom 10% to be exact, make roughly $24,000 a year, while the top 10% makes $108,000. (zippia.com)
- Overall employment of woodworkers is projected to grow 8 percent from 2020 to 2030, about as fast as the average for all occupations. (bls.gov)
- If your lumber isn't as dry as you would like when you purchase it (over 22% in Glen Huey's opinion…probably over 10-15% in my opinion), then it's a good idea to let it acclimate to your workshop for a couple of weeks. (woodandshop.com)
External Links
How To
How to join wood without using nails
Woodworking is an enjoyable hobby. You can make useful items from wood with your hands, which is both relaxing and fun. Sometimes you may want to join two pieces together of wood without using nails. This article will explain how to do this so that your woodwork projects stay beautiful.
The first thing you'll need to do is cut off any rough edges from your pieces of wood before joining them together. You don't want to leave sharp corners that could cause problems later on down the road. Now it's time to start glueing your boards together.
If you are working on hardwood, you should only use glue on one side. You should glue both sides if you are working with softwoods such as pine and cedar. Press the boards down until the glue is fully incorporated. After applying the glue, let dry the boards before proceeding to the next stage.
Once you've glued your boards together you will need to drill holes in the joints to accommodate screws. These holes will differ depending on the type and size of screw you are using. For example, if your screw is a 1/2-inch wooden screw, drill a hole that is at minimum 3/4 inches deep.
After drilling your holes, drive the screws into the board's backside. Don't hit the board's surface. You could damage the finish. When driving the screws, try to avoid hitting the ends of the screws too much. This will prevent splitting the wood's end grain.
You'll need to protect your completed project from the elements. You can seal the furniture pieces or cover the top. It doesn't matter what method you use, you want something that will last many years. You can choose from oil-based varnishes or polyurethane, shellac and lacquer as examples.
These products can be found in most home improvement shops. Make sure you get the right product for your job. Also, remember that some finishes are toxic and should never be used indoors. Wear protective gear whenever you are handling them.