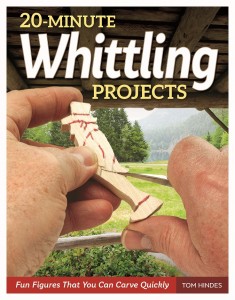
You should consider a few things when you are looking for an Oar Carving Knife. Size, sharpness of the knife, stag bone, lamination, as well origins should all be considered when purchasing a knife. This article will help you choose the best knife for your needs. After reading this article, you'll have an idea of what to look for when purchasing your new oar carving knife.
Size
The Oar Carver series of carving pocket knives is a classic and epitome of this craft. Three sizes are available in the current lineup. Version 2 has a longer blade and is thinner, while Version 3 has a thicker and wider blade. Here are some tips to help choose the right size.
Sharpness
The edge of your oar carver knife is an essential aspect. You should keep your knife's edge sharp. Your knife will begin to show signs of wear like chips, dullness and nicks. It is easy to determine the sharpness of an Oar Carving knife's edge by simply looking at it. A magic marker will help you match the angles of each knife's blade to its center.
Cut a piece off basswood to test its sharpness. A blade should be sharp enough to cut through wood without leaving any drag marks or ripples. A smooth cut is similar to cutting a baby's bottom with no marks. These marks indicate that the blade is not sharp enough to carve. Regularly check the sharpness and quality of your oar carving knife.
Laminated blades
The Oar Carver series has been the most popular example of a pocket knife for carving. It was designed by Ross Oar who is also a world-renowned carver. There are currently three versions: Versions 1 through 2. And 3. Each version is quite different from the one before it. Version 2 has a wider gap between the blades. It also has a shorter edge. The Oar Carver blade reference provides more details.
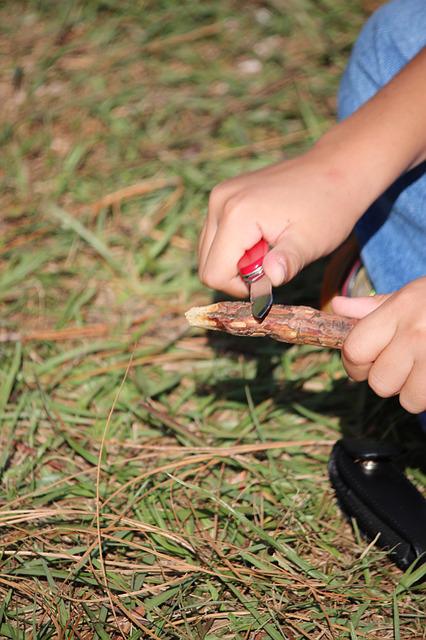
Mora produces two versions the 106 or 120. Both models have a laminated stainless steel blade. However, the Mora knife is slightly longer. Both knives come with a simple oval handle and a snap sheath. The Mora Frost 122 is another model that features a laminated carbon and steel blade with a 61 Rockwell-hardness. This knife is excellent for carving.
Origins
The oar carving knife was created in Japan from ancient times. The handle measures four and a quarter inches in length and is made from solid hardwood. The oar has an oar with a long, flat blade and a flat top. The knife's shaft measures 53 inches in length. The handle is carved into a narrow circle, while the blade and shaft are separated by a thin section of wood.
The oar is the earliest known carving tool, but its history is much longer. The oar was initially designed for coastal and riverine populations. Because of its widespread use and easy recognition, the Admiralty chose to use the oar symbol. Although the oar may have had different meanings, they are still useful. Below are some of its possible origins. If you are interested in learning more about the history and evolution of knife-making, they are also worth looking at.
FAQ
Can this be a way to make money?
Yes! Many woodworkers are already doing so. According to U.S. Bureau of Labor Statistics (BLS), woodworkers earned a median annual salary of $34,000 in May 2012. This is more than the national average of 31,000 per annum.
How can I tell what kind of wood I am working with?
Always read the label when purchasing wood. The label should provide information about the wood species, moisture content, and whether preservatives have been used.
How does a beginner woodworker earn money?
Many people learn how to make furniture in order to set up an online business. But if you're just getting started building furniture, there are other ways to earn money besides selling on Etsy. You could sell at craft fairs or local events. A workshop could also be offered for people who are interested to learn how they can build their own furniture. If you have the experience to be a carpenter, builder, or a designer, you may consider offering your services in remodeling homes or creating custom pieces.
Statistics
- The best-paid 10 percent make $76,000, while the lowest-paid 10 percent make $34,000. (zippia.com)
- Woodworkers on the lower end of that spectrum, the bottom 10% to be exact, make roughly $24,000 a year, while the top 10% makes $108,000. (zippia.com)
- If your lumber isn't as dry as you would like when you purchase it (over 22% in Glen Huey's opinion…probably over 10-15% in my opinion), then it's a good idea to let it acclimate to your workshop for a couple of weeks. (woodandshop.com)
- Overall employment of woodworkers is projected to grow 8 percent from 2020 to 2030, about as fast as the average for all occupations. (bls.gov)
External Links
How To
How to properly use your handsaw
To cut wood into pieces, a handsaw is used. Most common hand saws include circular saws (jigsaws), table saws and band saws. A hand saw is made from metal or plastic and cuts materials such as wood, plastics and metals.
A hand saw's main benefit is its ability make precise cuts at any angle, without the need to adjust it. They are also easy to sharpen, unlike power tools. But there are disadvantages. These devices are bulky and heavy so you need to be careful when transporting. Additionally, if they are unfamiliar, it is possible to injure oneself.
There are many different ways to hold a hand saw. While cutting, keep your fingers away from the blades. If you don't, you might get hurt. While holding the saw, make sure you place your fingers around its handle. Keep your thumb close to the blade. This will ensure that you don't accidentally touch or scratch the blade.
Use a hand saw only if you don't want anything to be under the piece of wood being cut. This would result in the blade slipping off the wood's surface. Before cutting, always inspect the area. Ensure no nails, screws, or other objects are underneath the wood.
While working with a saw, you should always use safety goggles. They keep dust out of your eyes, making it easier for you see what you are doing. Safety glasses protect your face against flying debris, which is another reason they are useful.
First, learn how to safely use a hand saw. Then, practice until you feel confident enough to start cutting things. Once you are comfortable with the basics, you will be able cut almost any material.